Storage Sheds Outlet is your one-stop destination for high-quality, affordable storage solutions designed to simplify your life and maximize your outdoor space. Whether you're looking to organize your backyard, create a functional workspace, or invest in a long-lasting shed that fits your style, weāre here to help.
Ā
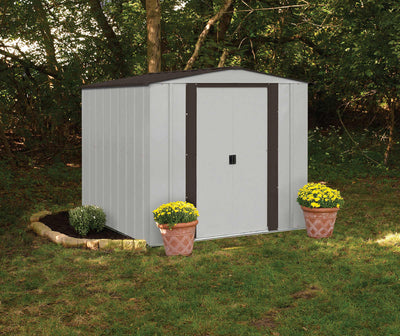
Select options
This product has multiple variants. The options may be chosen on the product page