Transform your shed into a comfortable, energy-efficient workspace by insulating with foam board – a cost-effective solution that delivers professional-grade climate control in your shed. Rigid foam insulation boards provide exceptional R-value per inch, create an effective vapor barrier, and can be installed in just a weekend with basic tools. Whether you’re creating a workshop, home office, or storage space, proper insulation prevents moisture damage, reduces energy costs, and maintains consistent temperatures year-round.
Select 1-inch to 2-inch thick extruded polystyrene (XPS) or polyisocyanurate boards for optimal thermal resistance, measuring your shed’s interior dimensions carefully to minimize waste. This project typically costs $200-$500 for an average 8×10 shed, delivering lasting performance that pays for itself through reduced heating and cooling expenses. With the right preparation and materials, you’ll create a properly insulated space that’s comfortable in any season.
Why Foam Board is Perfect for Your Shed
Types of Foam Board Insulation
When it comes to insulating your shed, you’ll find three main types of foam board insulation, each with its own unique benefits. Let’s explore these options to help you make the best choice for your project.
EPS (Expanded Polystyrene) is the most budget-friendly option and works well in most shed applications. It’s lightweight, water-resistant, and provides an R-value of about 4 per inch of thickness. While it’s not the strongest insulation, it’s perfect for basic shed needs and won’t break the bank.
XPS (Extruded Polystyrene) offers a step up in performance. Known for its distinctive blue or pink color, this type provides better moisture resistance and a higher R-value of around 5 per inch. It’s more durable than EPS and maintains its insulating properties better over time. For sheds in damp climates, XPS is often worth the extra investment.
Polyiso (Polyisocyanurate) boards offer the highest R-value per inch, typically around 6.5. This makes them ideal for sheds where space is at a premium, as you can achieve better insulation with thinner boards. While they’re the most expensive option, they’re also the most effective at temperature control. Polyiso boards usually come with a foil facing that acts as a built-in vapor barrier, adding extra protection against moisture.
Choose based on your climate, budget, and specific needs – there’s no one-size-fits-all solution when it comes to shed insulation.
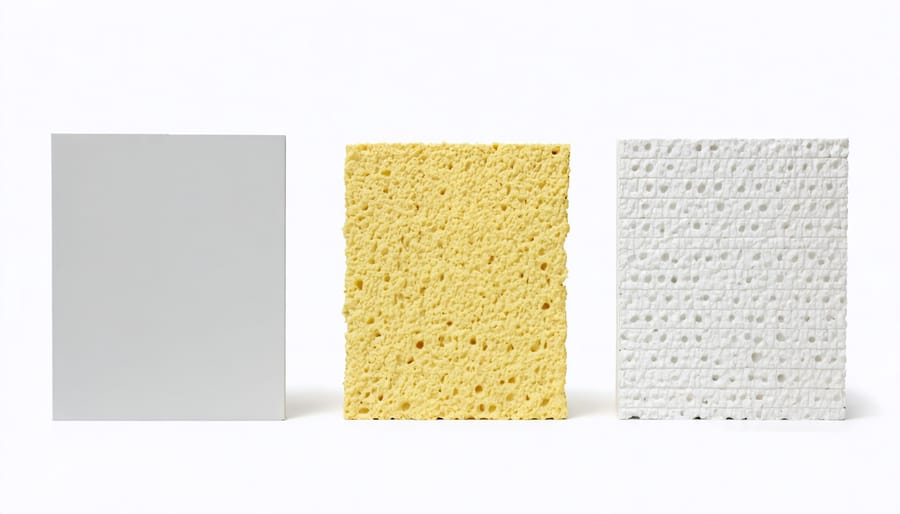
Required Tools and Materials
Before starting your shed insulation project, gather these essential tools and materials:
Materials:
– Foam board insulation panels (enough to cover walls and ceiling)
– Foil tape or specialized insulation tape
– Construction adhesive
– Vapor barrier (if not included in foam board)
– Wooden furring strips
– Screws and washers
– Caulk for sealing gaps
– Utility knife blades (several)
Tools:
– Measuring tape
– Utility knife with spare blades
– Straight edge or T-square
– Pencil for marking
– Drill with appropriate bits
– Caulk gun
– Safety glasses
– Work gloves
– Dust mask
– Sturdy ladder or step stool
– Level
– Scissors or shears
– Cleaning supplies
Optional but helpful:
– Foam gap filler
– Panel saw (for large cuts)
– Work table or sawhorses
– Assistant for handling large panels
Make sure to purchase approximately 10% more materials than your initial measurements indicate to account for mistakes and wastage. All materials should be stored in a dry place until you’re ready to begin the installation process.
Preparing Your Shed for Insulation
Moisture Check and Repairs
Before installing insulation, it’s crucial to thoroughly inspect your shed for any existing moisture problems. Start by checking the walls, floor, and ceiling for water stains, mold, or mildew. Pay special attention to corners and areas around windows and doors where moisture tends to accumulate. A moisture meter can help identify hidden dampness in the wood.
To effectively prevent condensation issues, address any leaks in the roof or gaps around windows and doors. Apply appropriate weatherstripping and replace damaged seals. If you spot any rotted wood, replace it immediately to maintain structural integrity.
Ensure proper ventilation by installing vents if needed, and consider adding a vapor barrier between the outer wall and insulation. Check that your shed’s foundation is slightly elevated from the ground, and verify that water drains away from the structure. If necessary, improve drainage by adding gravel around the perimeter or adjusting the grade of the surrounding soil.
Fix any gaps or holes in the exterior siding, and apply caulk where needed. This preparation work might take extra time, but it’s essential for the long-term success of your insulation project.
Wall Preparation Steps
Before installing foam board insulation, proper surface preparation is essential for the best results. Start by thoroughly inspecting your shed’s interior walls for any damage, holes, or gaps that need repair. Use wood filler or caulk to address these issues, ensuring a smooth surface for the insulation.
Next, clean the walls using a brush or vacuum to remove dust, cobwebs, and debris. Pay special attention to corners and areas where the walls meet the floor and ceiling. If you notice any signs of moisture or mold, address these issues first and ensure you have proper ventilation to prevent future problems.
Check that all electrical wiring is secure and properly positioned. If necessary, install additional blocking between wall studs to provide solid mounting points for the foam board. Remove any protruding nails or screws that might interfere with the insulation installation.
Finally, measure and mark your wall studs’ locations, as you’ll need these reference points when installing the foam board. A pencil and straightedge will help you create clear guidelines for accurate installation.
Step-by-Step Installation Process
Measuring and Cutting
Start by measuring your shed’s walls, ceiling, and floor areas carefully. Take multiple measurements to ensure accuracy, and don’t forget to account for windows, doors, and any obstacles. Add an extra inch to your measurements to allow for proper fitting and minor adjustments.
When cutting foam board, use a straight edge as your guide and score the board deeply with a utility knife. Make several passes rather than trying to cut through in one go. For precise cuts around outlets or pipes, create a paper template first and transfer the measurements to your foam board.
Pro tip: Cut your panels on a flat surface and always wear safety glasses. Keep your utility knife sharp for clean, precise cuts, and remember it’s better to cut slightly large than too small – you can always trim down if needed.
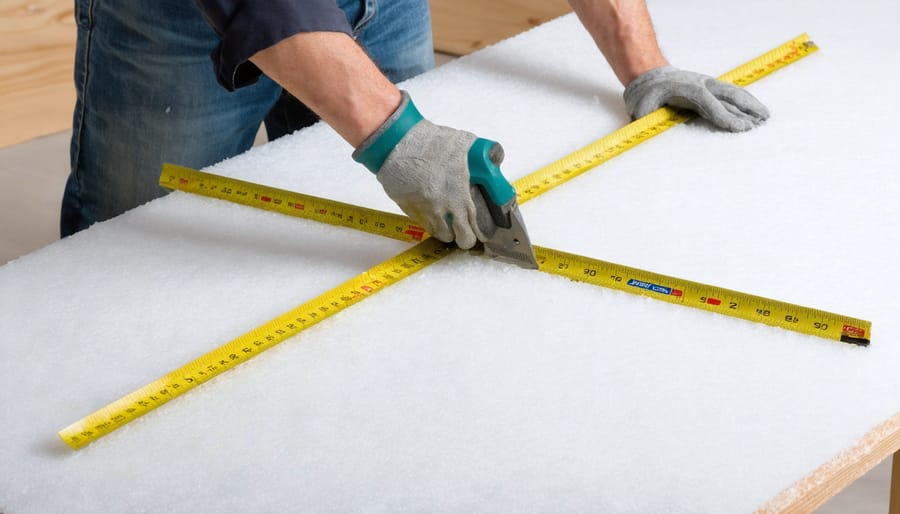
Securing the Foam Board
Once you’ve measured and cut your foam boards, it’s time to secure them to your shed’s walls and ceiling. Start by applying a construction adhesive in a zigzag pattern on the back of each board. Press the board firmly against the wall, ensuring it’s level and flush with adjacent pieces. While the adhesive sets, secure the board with 1-inch washers and screws every 12 inches along the edges and through the middle. For ceiling installation, use a helper to hold the boards in place while you fasten them. Remember to stagger the joints between boards for better insulation performance, and fill any small gaps with expanding foam. When working around electrical outlets or windows, cut precise holes in the foam board before mounting it to ensure a snug fit.
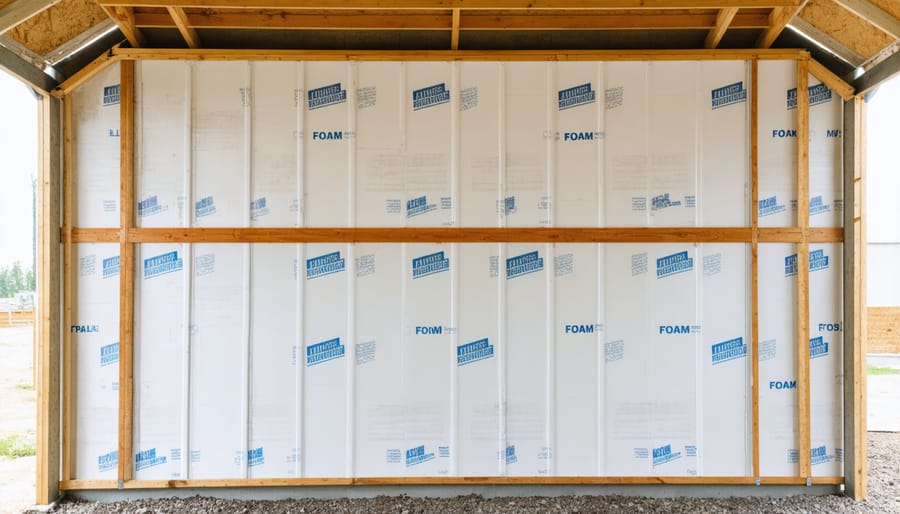
Finishing Touches and Weatherproofing
To complete your shed insulation project properly, focus on sealing any remaining gaps and ensuring long-term protection against moisture. Apply a high-quality silicone caulk around all joints, corners, and areas where the foam board meets the framing. This creates an airtight seal that prevents drafts and moisture infiltration.
Install a vapor barrier over the insulation if you haven’t already incorporated one. This additional layer helps prevent condensation from forming inside your shed. Pay special attention to areas around windows and doors, using weatherstripping to create tight seals.
Consider adding additional weatherproofing techniques such as drip edges above doors and windows to direct water away from vulnerable areas. If you’re planning to finish the interior, ensure proper ventilation to prevent moisture buildup.
Finally, inspect the exterior of your shed for any potential water entry points. Seal these areas with appropriate exterior-grade caulk or sealant. Remember to check these seals annually and repair them as needed to maintain your shed’s insulation effectiveness.
Insulating your shed with foam board is a worthwhile project that can transform your outdoor storage space into a more comfortable and energy-efficient area. By following the steps we’ve outlined, you can successfully complete this DIY project in a weekend. Remember to focus on proper measurements, secure attachment methods, and sealing all gaps for the best results. The initial investment in quality materials and time spent on careful installation will pay off through better temperature control and protection of your stored items. Don’t forget to address ventilation needs and check local building codes before starting. With your newly insulated shed, you’ll enjoy a more versatile space that’s protected from extreme temperatures year-round. Ready to get started? Gather your materials and tools, and transform your shed into a more functional space today!
Leave a Reply